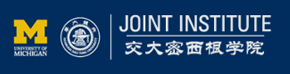
Student Projects
VE/VM450
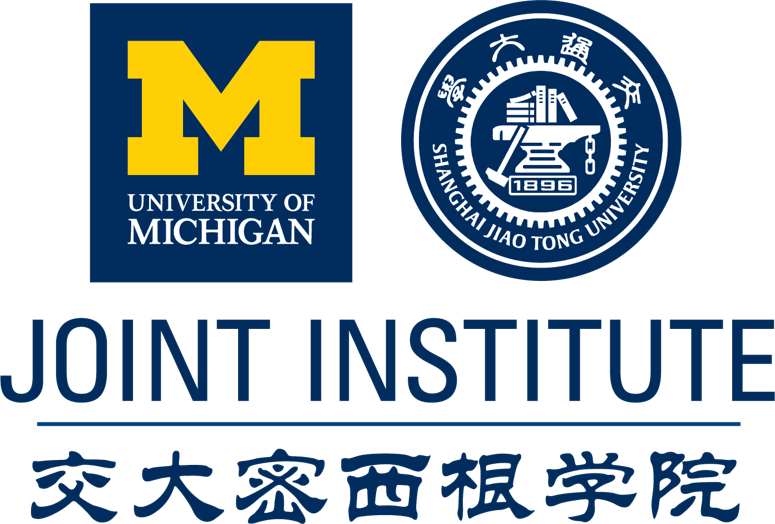
Sensor Fusion System for Automated Guided Vehicle
Instructors: Prof. Chong Han
Team Members: Binyu Xia, Jintian Ge, Xinyu Qian, Jiahao Wu, Jiaqi Wang
Project Video
Team Members
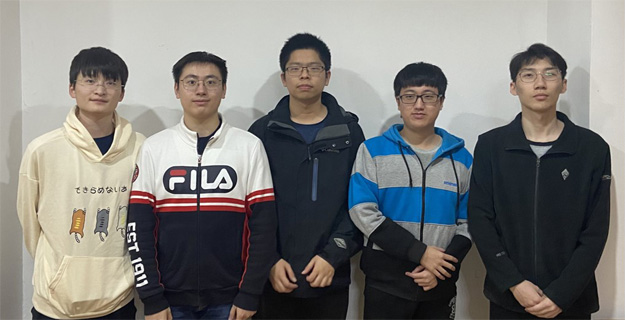
Team Members:
Binyu Xia, Jintian Ge, Xinyu Qian, Jiahao Wu, Jiaqi Wang
Instructors:
Prof. Chong Han
Project Description
Problem
With the development of industry, Automated Guided Vehicle (AGV) is introduced for increasingly large factory scale. It can carry and transport heavy materials according to a planned path. This project aims to build a cheap but precise navigation system for AGV, which will combine sensors including Inertial Measurement Unit (IMU) of high frequency (100𝐻𝑧) and Lidar and Camera of low frequency (10𝐻𝑧).
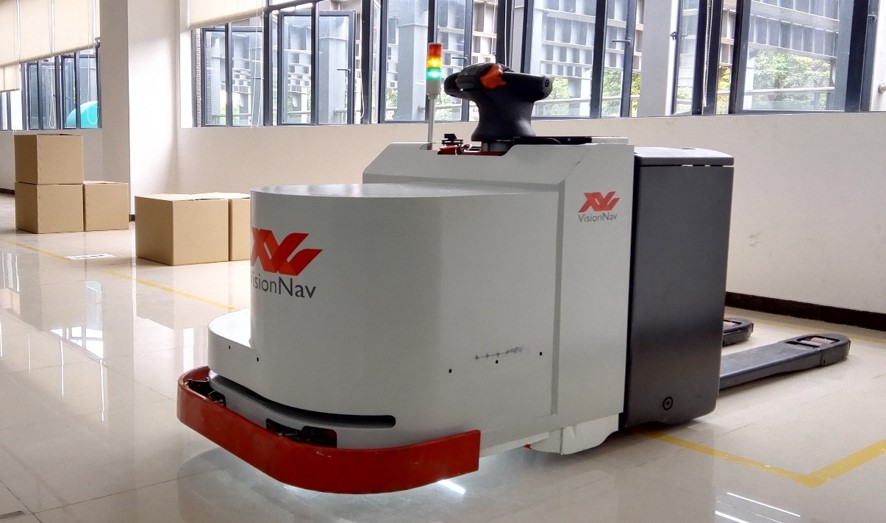
Fig. 1 Current AGV with vision guide [1]
Concept Generation
AGV sensor fusion system refers to the collection and analysis of information provided by both low frequency and high frequency sensors, so that it can estimate the position and orientation of the vehicle accurately and quickly.
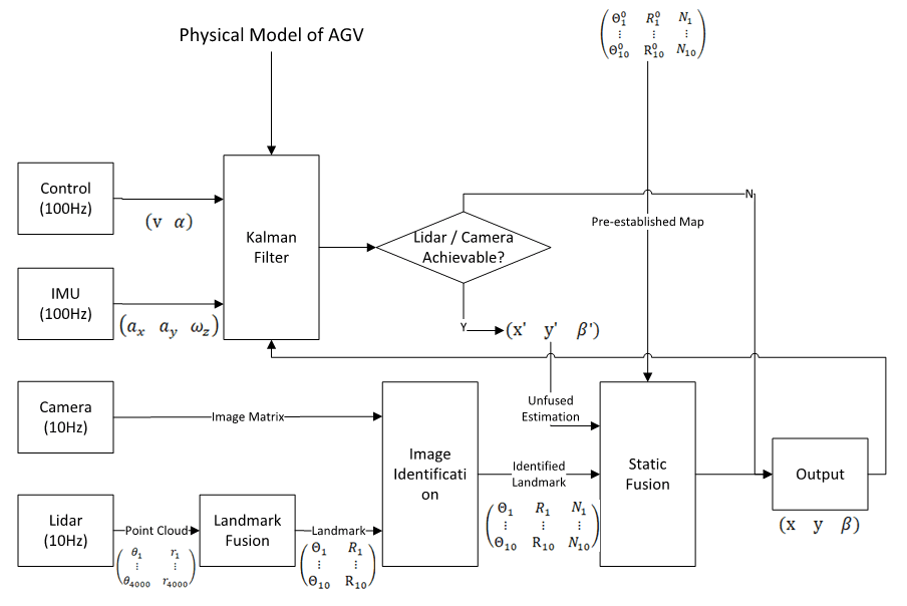
Fig. 2 Detailed structure function
Design Description
The bicycle model is used as our lateral vehicle motion model. A camera is installed in the front of the vehicle to capture the image. After the obstacles in the image are identified, the lidar on the top of the vehicle can measure the distance and the angle between the vehicle and the obstacles precisely at 10 𝐻𝑧. The IMU sensor on the vehicle measures the acceleration of three axes and angular velocity. By integrating the information, the position and orientation of the vehicle can be roughly estimated at 100 𝐻𝑧. A fusion algorithm is used to make a precise estimation at a high frequency.
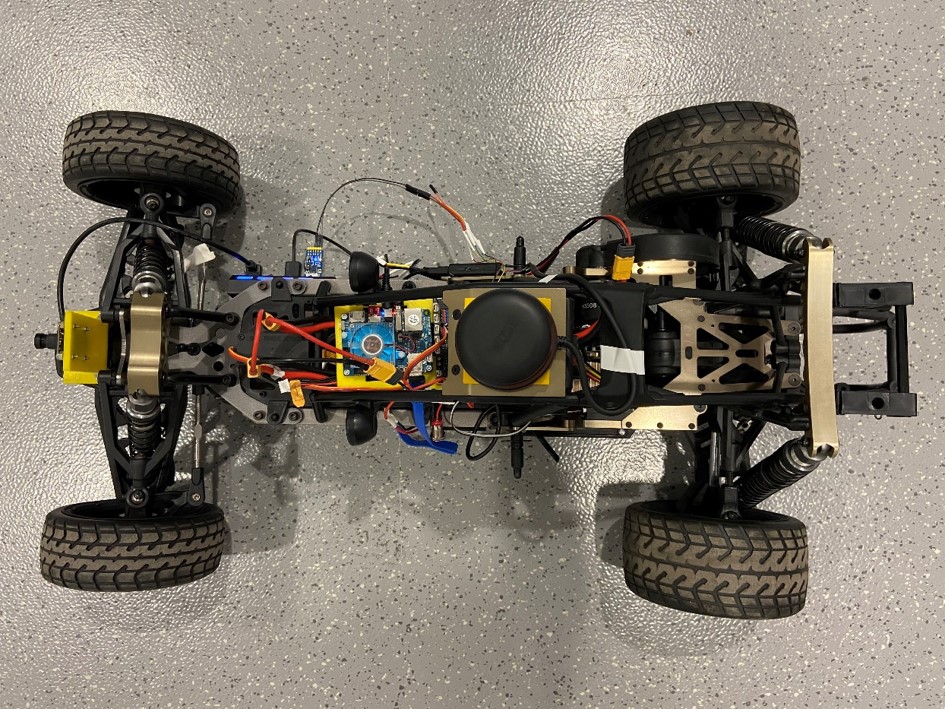
Fig.3 The whole set-up AGV
Modeling and Analysis
A Kalman filter algorithm is used to fuse the control signal and IMU signal to improve the estimation at 100 𝐻𝑧. A triangulation algorithm is used to estimate the position and orientation of the vehicle with the obstacle information provided by camera and lidar at 10 𝐻𝑧. The low frequency estimation will make compensation and correction to the high frequency estimation to guarantee the accuracy.
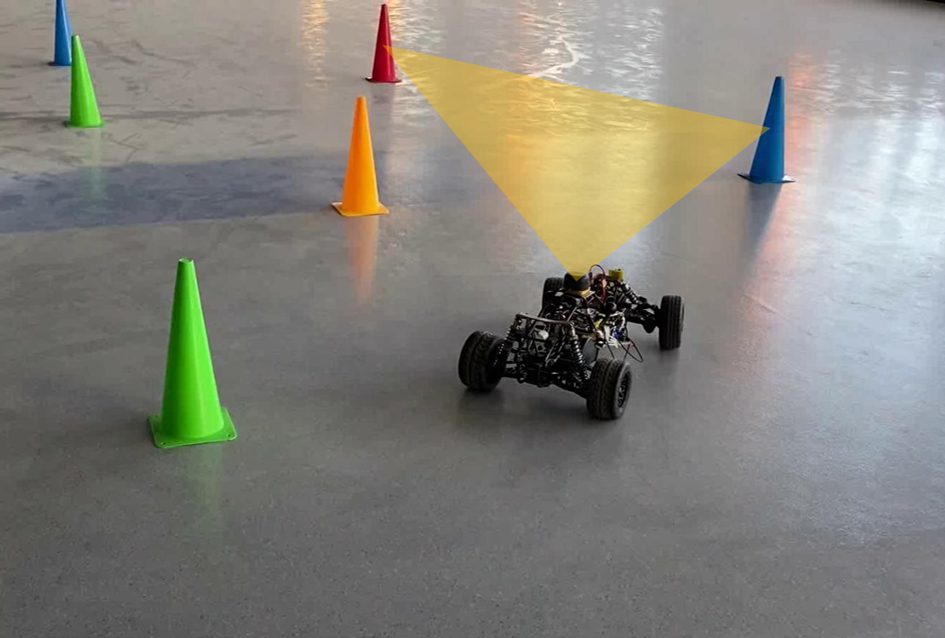
Fig. 4 Triangulation test
Validation
Validation Process:
The AGV runs in a ring test site with an inner radius of 2 𝑚 and an outer radius of 4 𝑚, where six obstacles are set in the inner radius sixteen obstacles are set on the outer radius. The AGV identifies the surrounding obstacles and estimate its position and orientation at 100 𝐻𝑧. The trajectory fitted based on the estimated results is consistent with the actual trajectory of the AGV, which means our estimation is correct.
Validation Results:
According to validation part, all the specifications can be met.
√ Delay of communication ≤ 3 𝑚𝑠
√ Precision of position ≤ 10 𝑐𝑚
√ Precision of angle ≤ 10 °
√ Response time ≤ 10 𝑚𝑠
√ Total cost ≤ 3000 𝑅𝑀𝐵
√ means having been verified.
The AGV runs in a ring test site with an inner radius of 2 𝑚 and an outer radius of 4 𝑚, where six obstacles are set in the inner radius sixteen obstacles are set on the outer radius. The AGV identifies the surrounding obstacles and estimate its position and orientation at 100 𝐻𝑧. The trajectory fitted based on the estimated results is consistent with the actual trajectory of the AGV, which means our estimation is correct.
Validation Results:
According to validation part, all the specifications can be met.
√ Delay of communication ≤ 3 𝑚𝑠
√ Precision of position ≤ 10 𝑐𝑚
√ Precision of angle ≤ 10 °
√ Response time ≤ 10 𝑚𝑠
√ Total cost ≤ 3000 𝑅𝑀𝐵
√ means having been verified.
Conclusion
IMU sensor and control signal can be used to make a rough estimation at a 100 𝐻𝑧 while the camera and lidar can be used to make a precise estimation at 10 𝐻𝑧. The key to achieve a precise and quick estimation is to generate a sensor fusion system, which can use the low frequency estimation results to compensate and correct the high frequency estimation results. Also, the use of Kalman filter algorithm and triangulation algorithm is important.
Acknowledgement
Sponsor: Prof. Mian Li from UM-SJTU Joint Institute
Prof. Chong Han from UM-SJTU Joint Institute
Chenzhi Zhang from UM-SJTU Joint Institute
Prof. Chong Han from UM-SJTU Joint Institute
Chenzhi Zhang from UM-SJTU Joint Institute
Reference
UM-SJTU JOINT INSTITUTE